About Demister
What is a demister?
The mist contained in gas has negative effects in various aspects, such as air pollution,
mechanical corrosion, and loss of raw
materials. The mist is mechanically generated
from each tower as scrubbers, cooling towers, and evaporaters has a quite big particle
diameter of tens ~ hundreds of microns.
And the mist generated through condensation and chemical reactions of gases is very fine.
A demister, also called a mist eliminator, wire mesh separator, or wire mesh blanket, is a type of filter that separates and removes mist or dust contained in a fluid or gases. and It’s also a reaction activator that effectively makes a reaction. The demister is also semi-permanent because it is manufactured using various materials depending on the usage conditions, and its simple structure makes it easy to install and repair, making it a very economical product.
A demister, also called a mist eliminator, wire mesh separator, or wire mesh blanket, is a type of filter that separates and removes mist or dust contained in a fluid or gases. and It’s also a reaction activator that effectively makes a reaction. The demister is also semi-permanent because it is manufactured using various materials depending on the usage conditions, and its simple structure makes it easy to install and repair, making it a very economical product.
Structure
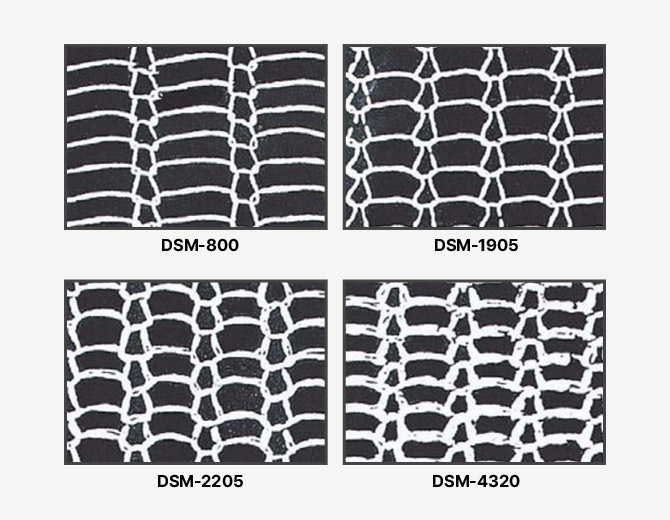
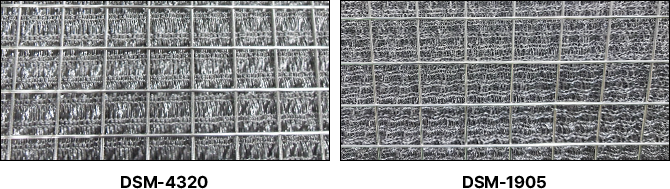
How it works
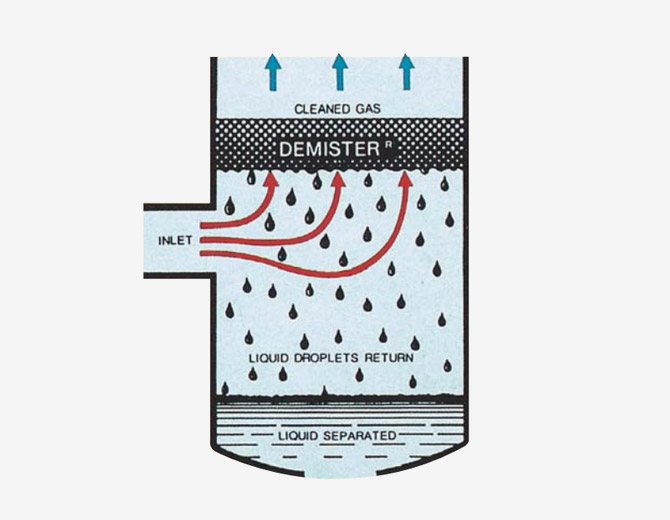
The right figure shows the operating principle
of the demister working on an evaporating system.When the gas generated from the liquid (L) turns into bubbles (V) and these bubbles rise up, at this time, the surface of the liquid bursts and minute particles of the liquid are generated and accompanied with gases, which go through the demister. The minute
particles, before going through the demister, get to have big volume due to the inertial
collision principle on the surface of a pad.
The particles containing foreign materials fall down due to weight and the gases or the gases containing the liquid components that have gone through the demister become pure gases that impurities are perfectly removed,
and then, they go out of the demister.
Features by Demister style
DSM-800 | Usgae conditions for the case that high
velocity and low pressure drop is required,
or collecting larger particles, no need high efficiency. It’s used for general collection efficiency. (Heavy processing type) |
---|---|
DSM-1440 | The type is widely used in petrochemical
plants and as a standard type for general
efficiency purposes. Pressure drop is relatively small, and the collection Efficiency is typically 90 to 99%. (Standard type) |
DSM-1905 | Most commonly used as a High-efficiency
Standard type. Generally, it has an collection efficiency of 90 to 99% for particles of about 10micron. (High-efficiency standard type) |
DSM-3903 | Twice the structure of standsrd type. In
particular, it’s used for high efficiency is
required. The Pressure drop may increase, but efficiency is over 90% at a low velocity 1 m/sec or less |
DSM-2205 | Used to collect fine particles of about 3micron In particular, in the case of low concentration, when the quanity of mist (dust) is less than 10 g/m³, the collection efficiency can be doubled as the thickness is increased. ( High -efficiency type ) |
DSM-4320 | Used for collecting ultrafine particles Measuring less than 0.5–1 micron; higher effectiveness than the DSM-2205 style can be achieved. (Ultra high-efficiency type) |
DSM-JM | Manufactured as a composite structure
of DEMISTER element, according to the usage
conditions. High-efficiency performance is required under limited usage conditions |
Material
Various materials can be used for manufacturing depending on the application. The main materials are as follows:
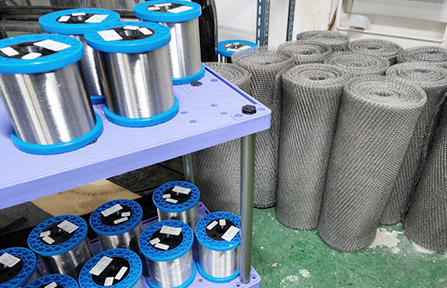
Stainless Steel ( STS304, STS316, STS316L ),
Monel, Duplex, etc.
Monel, Duplex, etc.
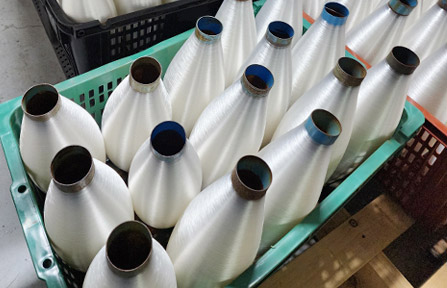
P.P (Poly Prorylene), P.E (Poly Ethylene),
HPE, etc.
HPE, etc.
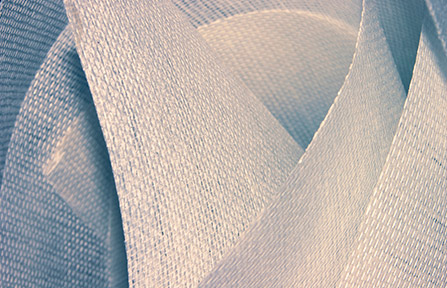
Glass Fiber
Performance
01
Air pollution
prevention
prevention
Removing harmful substances from gas
02
Improving
product purity
product purity
Removing impurities from gas
03
Cost reduction
Preventing the scattering of the product’s raw materials
04
Extending plant life
and providing an
energy-saving effect
and providing an
energy-saving effect
Collecting mist separately by installing in the pre- and post-plant processes